After-sales problems are a topic that no commodity can escape. Excellent companies like Apple and Mercedes-Benz also need to deal with after-sales issues. Europe and North America are our main exporting markets. The local labor and maintenance costs are very high there. If there is a batch problem in the product, it will bring serious losses to both us and our customers. When dealing with after-sales problems, our philosophy is: to avoid quality problems to the greatest extent possible from the very source.
Our Product Quality Standards
Before listening to a supplier on how to guarantee after-sales problems, why not see how they control quality problems? Quality has always been our company’s No.1 priority. Our products all strictly follow these quality standards:
Ambient temperature & Humidity
In addition, you need to pay special attention to this: any refrigeration configuration has its specific application environment. Some problems may arise if the equipment is used beyond its intended environment. For example, the cooling temperature is not enough, too much condensation water, and so on. The applicable environment mainly includes ambient temperature and humidity. Ambient temperatures are divided into N, ST, and T types based on product size and style. Our product is suitable for humidity below 60% RH. If your environment goes beyond that, you need to tailor your product to your specific environment to avoid problems.
How We Guarantee The Quality Standards
We are ISO9000 and ISO14001 approved. Meanwhile, our company is operated under the ERP system and strictly follows the below procedures to guarantee quality:
Besides, since we only export and mainly in Europe and North America, our whole company has a good awareness of quality and surely applies more strict standards. Also, our workers take professional training programs 1~2 times per month, as our company emphasizes this a lot and put a lot of money into it to safeguard both of our business.
Our Warranty Term
We apply 3 years warranty for the compressor and 1 year for the whole body. Meanwhile, we will provide 1% FREE spare parts together with your order in case of maintenance, and are committed to providing parts throughout the whole product lifetime.
Note: Our product quotations only include this after-sales clause by default, and do not include other costs like transportation or local maintenance.
Classification of Quality Problems
According to the nature and severity of the problem, we divide quality problems into the following 3 levels:
Class A: Safety defects (which define any defect not complied with CB safety regulations or something threatening the personal security of the end-user.)
Class B: Structural and cooling performance defects (which define any defect like leakage or blockage in the cooling system, poor connecting wiring, wrongly used compressor or thermostat, damage on the cabinet or door frame liner, foaming vacuole of the cabinet or door, serious distortion of the cabinet, failure or damage on switches, damage on exterior plastic items, etc.)
Class C: Appearance defects (which define any defect causing some end users’ complaints like dirty, uncleaned foaming, little fray or scratch, small shrinking marks on the plastic parts or painting metals, bulging or dent for minor important areas, the gap in stitching, rusting, etc.)
Quality Complaint Resolution Process
Documentation
Grow Your Business with Us Now
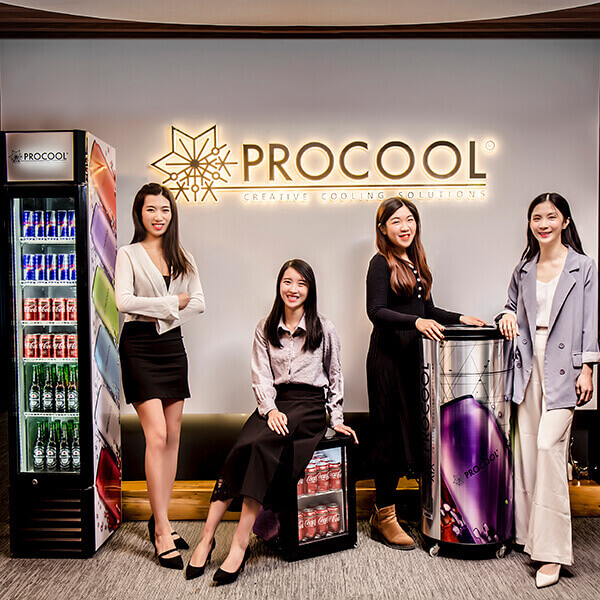
Grow Your Business with Us Now
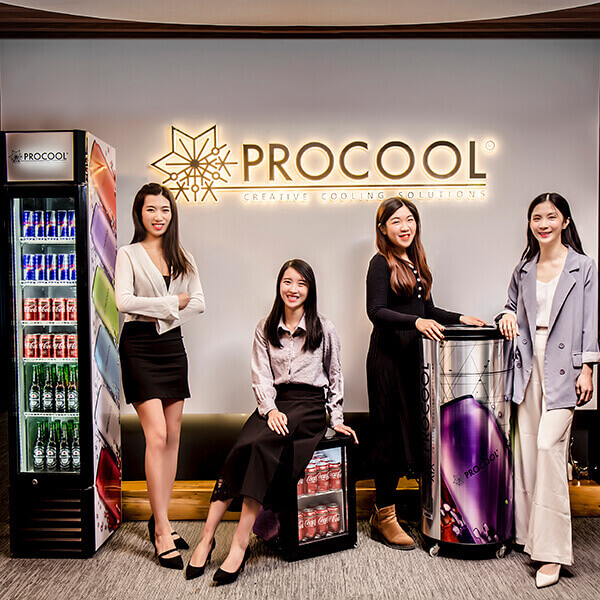